SPAIN
GERMANY
FRANCE
ITALY
DENMARK
GREECE
Participating partners
The Greek cMDF consists of two partners: AidPlex (a Greek medical start-up) and CERTH (a Greek research institute, with important scientific and technological achievements in various fields).
Scope and purpose of the cMDF
The Greek cMDF aims to bridge the gap between SMEs and makerspaces in various collaborative product development projects by organising innovative workshops. AidPlex, with expertise in medical sector, will offer better treatment experience to potential customers. Apart from medical sector, CERTH will expand the provided services on micro-manufacturing and rapid prototyping to several sectors, such as robotics, agile tools, electronics and consumer lifestyle goods.
Expansion strategy
The Greek cMDF has organised and will continue organizing remote and physical events for local SMEs and the public (citizens) at OK!Thess.
Expansion for start-ups:
Preliminary interest has already been gathered from start-ups and makers that wanted to expand their network of customers, improve their communication with them in order to create future partnerships. If prototyping sessions with start-ups (providing ideas) are successful, maturation of the prototypes will be followed as a co-creation and co-design activity.
Expansion to customers:
After learning about the interests of SMEs, these topics will be deepened. Involved SMEs will also promote Greek cMDF’s activities and projects into their existing networks and public relations channels, sharing to local and regional level the values of social manufacturing and iPRODUCE.
Key services
The main services offered by the Greek cMDF are:
|
|
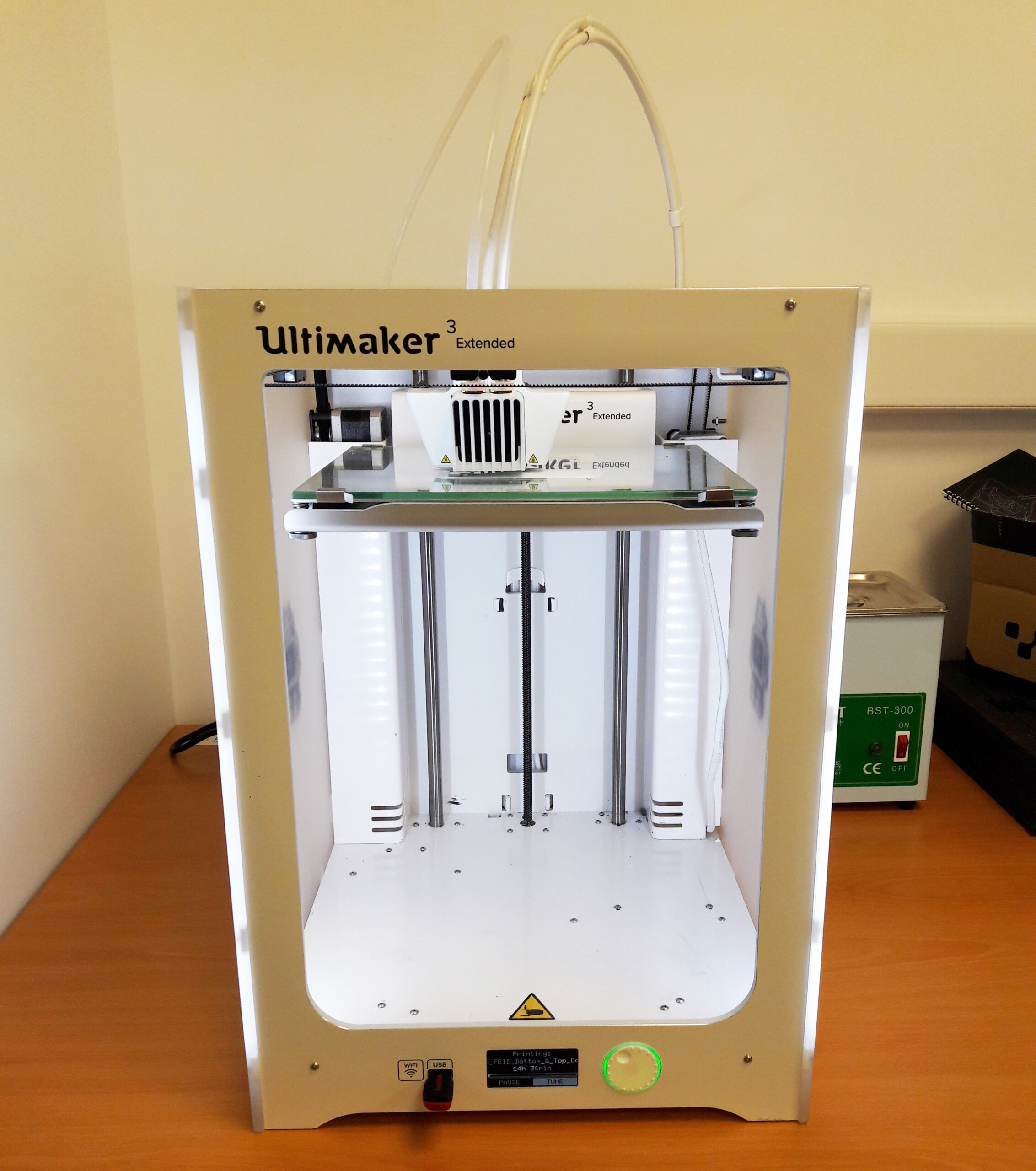
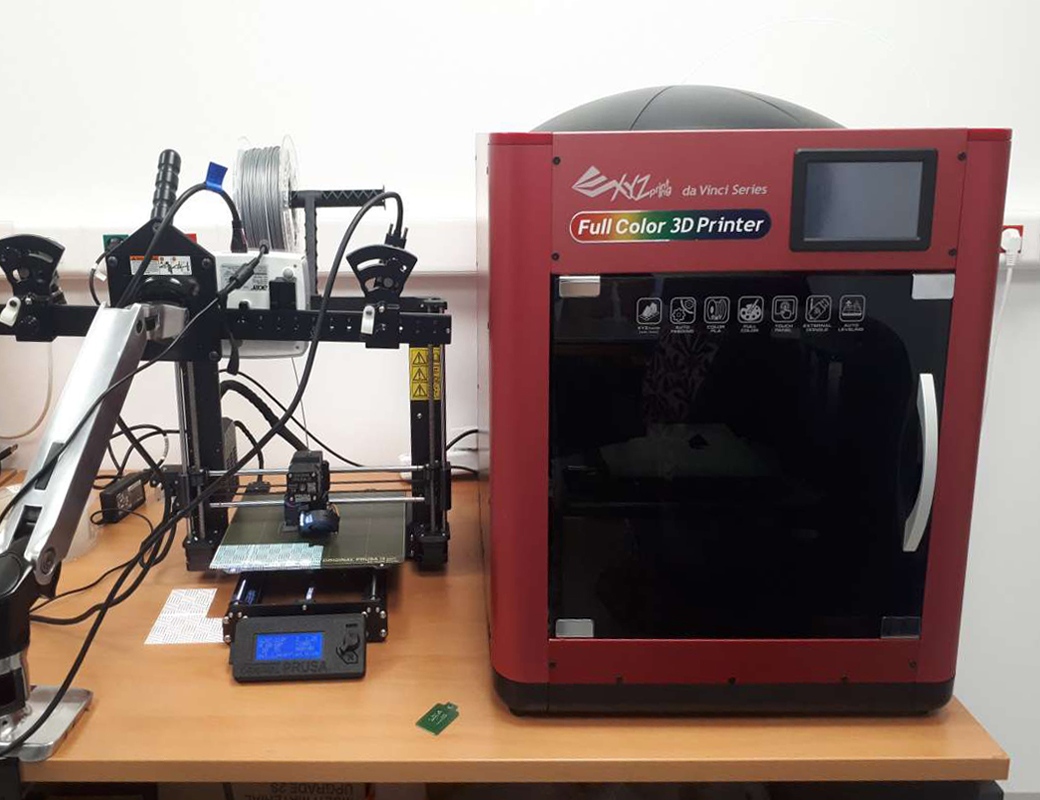
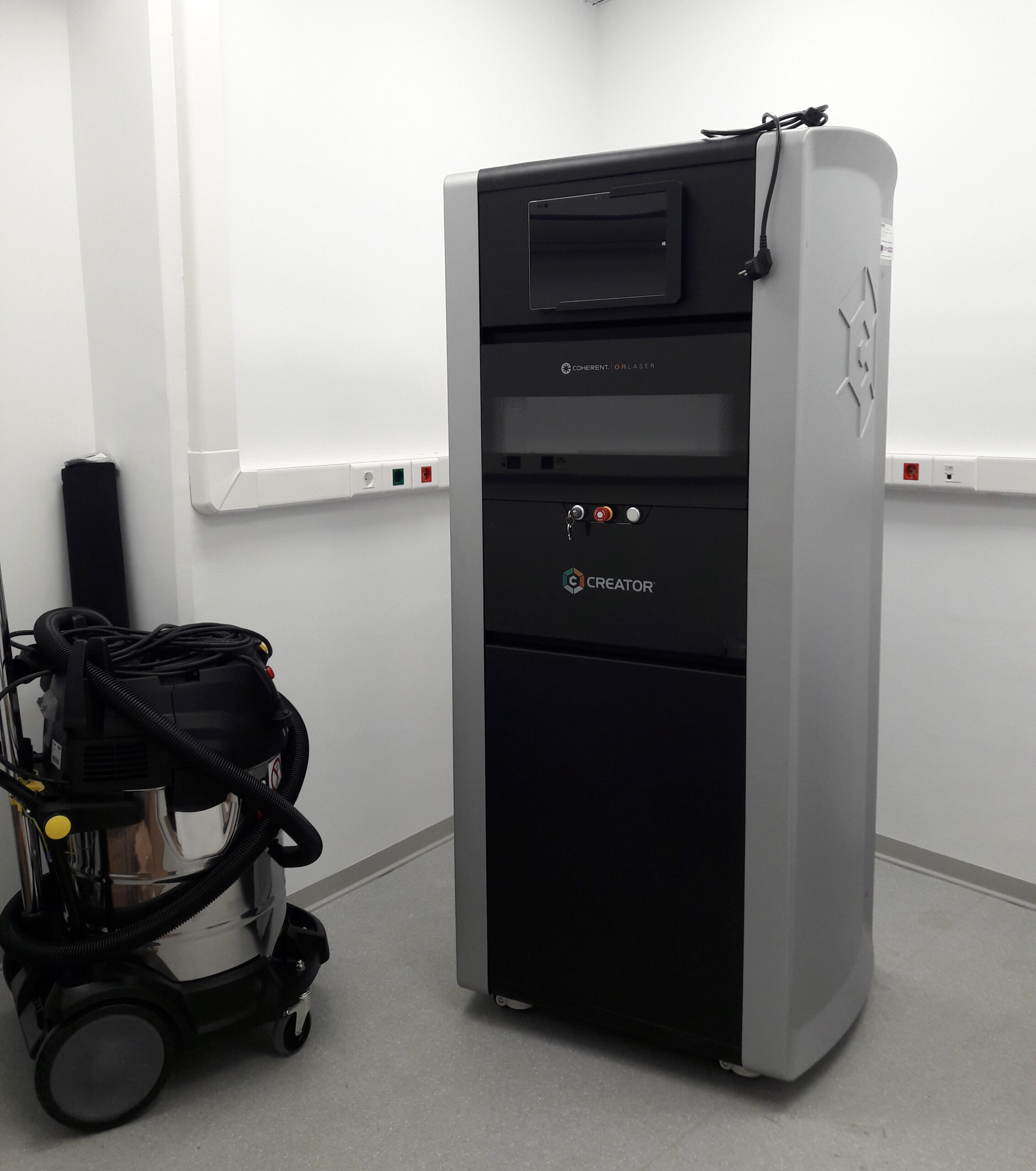
Greek cMDF use cases
UC1: IoT based orthopaedic back brace
Description of the use case
Until now, back braces for scoliosis have been very uncomfortable and clinicians can't track patients' progress, increasing the risk of possible spine surgery in the future. The orthopaedic back brace solution is designed by AidPlex with the aim of higher comfort levels and retrofitting the resulted design with IoT sensors, for scoliosis, kyphosis, or similar spinal deformities. The overarching goal is to fine-tune the design of a back brace by examining aspects like weight distribution, modularity, size, adaptability, and overall comfort, whilst IoT sensors will help patients self-assess and adapt their back braces leading to higher degrees of adherence and outcome. The IoT component of the solution will also support gamified processes, which stand to help patients follow through treatment and exercise more diligently, achieving better results and subsequently increase their quality of life.
Objectives
AidPlex is looking for innovative features to improve existing solutions. The Greek cMDF provides to any existing orthopaedic back brace integration of an IoT system.
Patients and physicians are expecting a more efficient back brace. Also, gamification is expected to help children make the wearing habit more joyful and effective.
Methodology
Through the cMDF profiling marketplace provided by the iPRODUCE OpIS platform, AidPlex will establish a contact and a working relationship with the cMDF, by bringing to their attention that target users are demanding a better treatment experience, which will be more acceptable by the patients/children. Doctors and children will select the features: size, color, and type of the straps. AidPlex will conduct desk research and then will ask for healthcare practitioner’s feedback on AidPlex’s assumptions.
Design thinking usually includes the following processes and activities: (1) empathise, (2) define, (3) ideate, (4) prototype, and (5) test. After the design thinking stage, a design brief is elaborated with the selected new product idea. AidPlex’s engineers will start developing the 3D models. Then, AidPlex will print the first 3D models in order to test them with children and their families. With the AR/VR system, AidPlex will demonstrate the proposed solution to parents and their children to achieve a better understanding of the solution and give them the chance to select their favourite features.
Expected results
- Increased ratio of ideas related to new innovative products brought to market.
- Reduced the product's development cost.
- Increased the company’s portfolio of innovative products.
- Improved the adequacy/effectiveness of the idea from its original state due to the focus group feedback.
- Raised co-creation practices between the industry and users.
- Consumer goods sectors addressed: Medical and IoT.
- Demand-driven sharing economy business models in the medical sector.
- Customer-driven products manufactured in the Greek cMDF.
- Validated, market ready (business model and plan) for IoT based orthopaedic back brace.
- Overall labour effectiveness.
- Compatibility with the digital iPRODUCE platform (OpIS).
UC2: Splints for fractures
Description of the use case
Until now, splinting and casting of fractures require a high amount of resources, such as time and consumables, generating significant medical waste. AidPlex, doctors, and patients are going to design new sizes and designs for children in order to provide the best possible treatment experience. Patients can select the size, colour and type of strap for the splint. The main features of the splint are their waterproof, lightweight, and skin-friendly nature. Firstly, patients can easily bathe themselves without the use of plastic covers around their broken bones. In addition, the splints offer a six times lighter solution, giving patients a more useful splint during the treatment period. AidPlex’s splint has many holes, therefore patients’ skin can breathe normally and eliminate the chance of skin irritation problems. Our quick and easy-to-apply solution helps healthcare professionals do their job easier.
Objectives
AidPlex, supported by CERTH, is looking for innovative ways to deliver patient-centred products and expand the portfolio of customisable products that can differentiate them from their competitors. Users are expecting a more efficient children splint, both for doctors and children.
Methodology
Through the cMDF profiling marketplace provided by the iPRODUCE OpIS platform, AidPlex will establish a contact and a working relationship with the cMDF, by bringing to their attention that target users are demanding a better treatment experience, which will be more acceptable by the patients/children. Doctors and children will select the features: size, color, and type of the straps. AidPlex will conduct desk research and then will ask for healthcare practitioner’s feedback on AidPlex’s assumptions.
Design thinking usually includes the following processes and activities: (1) empathise, (2) define, (3) ideate, (4) prototype, and (5) test. After the design thinking stage, a design brief is elaborated with the selected new product idea. AidPlex’s engineers will start developing the 3D models. Then, AidPlex will print the first 3D models in order to test them with children and their families. With the AR/VR system, AidPlex will demonstrate the proposed solution to parents and their children to achieve a better understanding of the solution and give them the chance to select their favourite features.
Expected results
- Reduced product development cost.
- Increased the company’s portfolio of innovative products.
- Improved the adequacy/effectiveness of the idea from its original state due to the focus group feedback.
- Raised co-creation practices between the industry and users.
- Consumer goods sectors addressed: medical
- Customer-driven product manufactured in cMDF (AidPlex).
- Open innovation missions where collaborative manufacturing will be applied: collecting feedback from (a) doctors/clinicians and (b) patients.
- Demand-driven sharing economy business models in the medical sector.
- Validated, market-ready (business models and plans) product.
- Overall labour effectiveness.
- Compatibility with the digital iPRODUCE platform (OpIS)
UC3: Splints for pets
Description of the use case
Until now, splinting and casting of fractures require a high amount of resources, such as time and consumables, generating significant medical waste. AidPlex and veterinarians are going to develop new designs for pets, in order to provide the best possible treatment experience. In addition, the owners can select the size, colour and type of strap for the splint. The main features of the splint are their waterproof, lightweight, skin-friendly, and eco-friendly nature. First of all, pets can be bathed easily without the use of plastic covers around their broken bones. AidPlex’s splint is perforated, therefore pets’ skin can breathe normally and eliminate the chance of skin irritation problems. Sometimes, pets pee on their splint and then it must be changed. Our waterproof, quick, and easy-to-apply solution helps veterinarians do their job easier.
Objectives
AidPlex, supported by CERTH, is searching for innovative ways to deliver patient-centred products and to expand the portfolio of customizable products that can differentiate them from their competitors. Users are expecting a more efficient pet splint, both for veterinarians and pets.
Methodology
xxx
Expected results
- xxxx
UC4: Customised face shields
Description of the use case
Customised protective face shields were designed and fabricated for adults in the fight against COVID-19. The face shield is one of several projects being run by the COVID-19 Response Greece action. This project aims to make the design of protective gear open source and available to everyone that has relevant production facilities, under the license terms of Creative Commons (4.0 International License) Attribution-Non-Commercial, offering high levels of protection. After discussions with hospitals for kids and adolescents and refugee NGOs, AidPlex realised that all the solutions in the market are designed for adults. So, in order to offer high levels of protection to kids, AidPlex will design custom face shields to perfectly fit kids’ sizes.
Objectives
Users are expecting a more efficient face shield for children, providing a better treatment experience to patients during the pandemic and other difficult medical circumstances.
Methodology
xxx
Expected results
- xxxx
UC5: 3D printed luminous smart artefacts
Description of the use case
Under the COVID-19 pandemic, CERTH's Additive Manufacturing Unit (AMU) encourages students to fabricate 3D printed prototypes based on customised and personalised solutions, using Additive Manufacturing technologies. Students can co-create with AMU experts, 3D printed smart luminous artefacts based on their favourite historical and mythological figures. The goal of this product is to enhance educational and medical purposes and boost student’s psychology and creativity.The product is composed of three parts fabricated via three different AM technologies: (1) stereolithography (SLA) for the artefact, (2) fused filament fabrication (FFF) for the electronics housing, and (3) inkjet technology for the printed circuit board (PCB). The 3D printed smart luminous artefact is controlled by a user-friendly specialised mobile application (i.e. AMU4you).The student can select the preferred colour, brightness and blinking pattern, based on the selected mood or activity and use it as an controllable table lamp.
Objectives
CERTH will provide rapid and functional PCB, customised prototypes and of 3D printed figures by enabling experience with state-of-the-art additive manufacturing and IoT technologies.
Methodology
Through the cMDF profiling marketplace provided by iPRODUCE's OpIS, CERTH will establish contact and a working relationship between the cMDF and the potential user, facilitating the process of targeting users and also meeting their needs by adjusting the specifications. Students/ makers select specific features.
CERTH starts with a design thinking process, which includes: empathetic understanding of trends and market needs, analysis of possible problems and challenges to address the specific user’s needs, ideation (brainstorming and mind mapping methods), and prototyping.
Next, a design brief is elaborated with the selected new product idea. CERTH’s staff and researchers will develop the 3D models of the artefact and of the electronics housing, using the appropriate CAD software programs. Then, CERTH will export the 3D CAD model to the desired file format and adjust the parameters according to the CERTH equipment (e.g. FDM, SLA, PCB printer) that will be used for the manufacturing process. The prototype will be manufactured according the suitable 3D printing process. The next step involves set up of electronics, components and necessary parts. And the final step is the assembly of the prototype and testing of its functionality.
Expected results
- Consumer goods sectors addressed: a) educational, b) creative industry, c) IoT
- One customer-driven product manufactured in cMDFs (CERTH)
- Open innovation missions where collaborative manufacturing will be applied: feedback from: a) students, b) teachers/ parents and guardian’s association, c) makers, d) gamers, e) electronic engineers
- Overall labour effectiveness, gained by Generative Design Platform and AR/VR Toolkit inputs
- Compatibility with Digital iPRODUCE platform (OpIS)
UC6: 3D printed (bio) scaffolds
Description of the use case
CERTH's Additive Manufacturing Unit (AMU) encourages researchers to design and fabricate customised scaffolds with optimal lattice structures using additive manufacturing technologies for bio-applications, such as organoids or implants, to better understand neurological or other disorders/ diseases (e.g., Parkinson’s, Alzheimer’s disease) and screen potential treatments. The 3D printed scaffolds can be manufactured using different 3D printing technologies, such as: fused deposition modelling (FDM) technology, stereolithography (SLA), selective laser melting (SLM), and 3D Bio-printing.
Objectives
The objective of the use case is to provide rapid and functional 3D printed scaffolds (e.g., implants, organoids) and customised models/ protoplasm for bio-experimental procedures (e.g., Parkinson’s, Alzheimer’s disease) for personalised medicine.
Methodology
Through the cMDF profiling marketplace provided by iPRODUCE's OpIS, CERTH will establish contact and a working relationship between the cMDF and the potential user, facilitating the process of targeting users and also meeting their needs by adjusting the specifications. Researchers will select specific features, such as: size of the scaffold and the lattice structure of scaffold. CERTH starts with a design thinking process, which includes empathetic understanding of trends and market needs, analysis of possible problems and challenges to address the specific user’s needs, ideation (brainstorming and mind mapping methods), and prototyping. Next, the design brief is elaborated with the selected new product idea. CERTH’s staff and researchers will develop the 3D models of the scaffold, using the appropriate CAD software programs. Then, CERTH will export the 3D CAD model to the desired file format and adjust the parameters according to the CERTH equipment (e.g., FDM, SLA, SLM, Bio-Printer) that will be used for the manufacturing process. The prototype will be manufactured according the suitable 3D printing process. With an AR/VR system, CERTH will demonstrate the proposed solution to potential users in order to achieve better understanding of the solution via the visualisation of the product and give them the chance to select features or their preference.
Expected results
- Quick prototyping cycles and know-how transfer for implants and organoids
- Consumer goods sectors addressed: a) Medical
- One customer-driven product manufactured in cMDF (CERTH)
- Open innovation missions where collaborative manufacturing will be applied: feedback from: a) researchers, b) biologists, c) doctors/clinicians/surgeons, d) individuals, researchers (in medicine, pharmacy etc.)
- Overall labour effectiveness, gained by generative design platform and AR/VR Toolkit inputs
- Compatibility with the digital iPRODUCE platform (OpIS)